Cement is a fundamental material for building and construction in civil engineering. It has high adhesive properties when mixed with water and aggregates. As urbanisation, industrialisation and infrastructural development continue to increase, so has the use of cement.
Because cement manufacturing is a high volume process, any potential environmental impact would consequently be high. It is therefore pertinent that the environmental impact of the cement industry should be given due attention as it is bound to be a key player if the sustainable development goals (SDGs) are to be achieved.
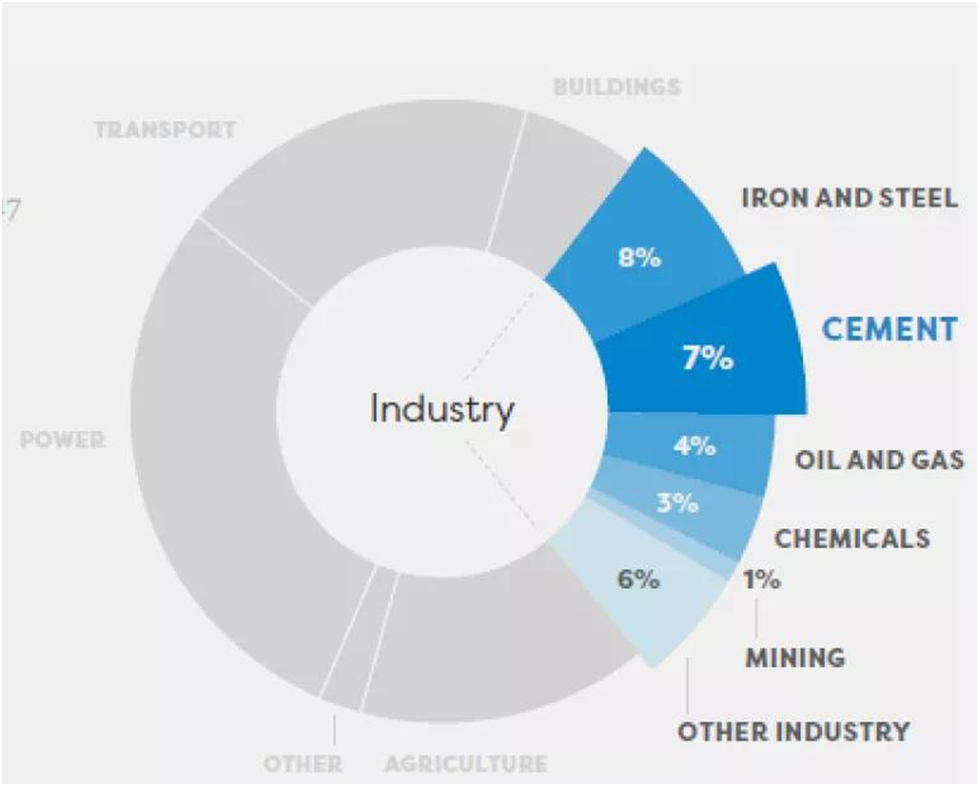
What is Cement?
Cement is a fine, soft, powdery-type substance, mainly used to bind fine sand and coarse aggregates together in concrete. Cement is a glue, acting as a hydraulic binder, i.e. it hardens when water is added.
How Cement is Made?
Cement manufacturing is a complex process that begins with mining and then grinding raw materials that include limestone and clay, to a fine powder, called raw meal.
The powdered limestone and clay are then heated to a temperature as high as 1450 °C in a kiln. The high-temperature process, known as calcination (clinker production), converts calcium carbonate (CaCO3), the principal component of limestone, to calcium oxide (CaO) or lime, releasing CO2.
During the process, the chemical bonds of the raw materials are broken down and then they are recombined into new compounds. The result is called clinker, which are rounded nodules between 1mm and 25mm across. The clinker is then grounded to a fine powder in a cement mill and mixed with gypsum to create cement.
Impact of Cement Manufacturing on Environment
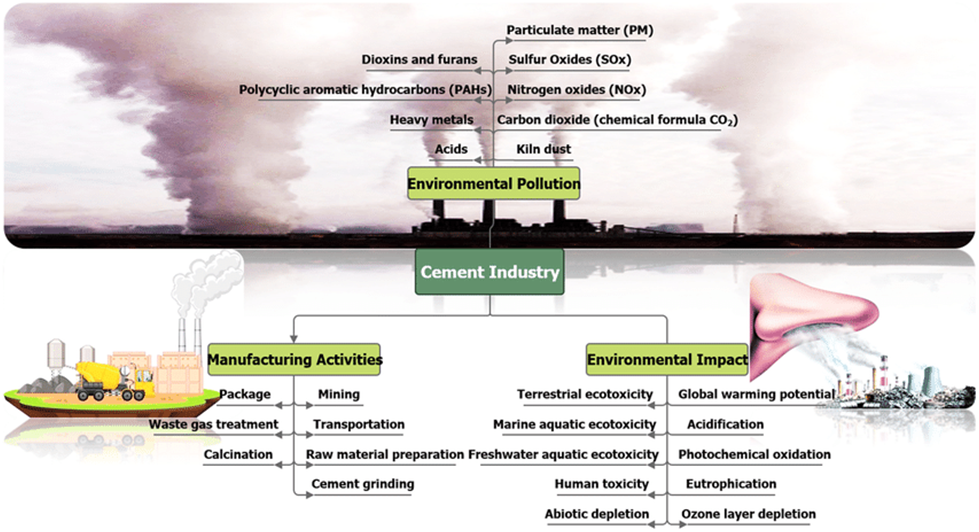
The cement industries are a major contributor to air and solid waste pollution.
Global warming and climate change: the role of the cement industry
The cement industry has been a major player in global warming and currently still is. Why? It is because the manufacturing process is one that generates lots of CO2, most of which cannot be harnessed. Global cement manufacturing is responsible for about 7% to 8% of the world’s total CO2 emissions.
About 40% of the CO2 emissions from cement manufacturing (dry process) comes from the combustion of fossil fuels in the kiln process while 50% comes from the roasting of limestone.
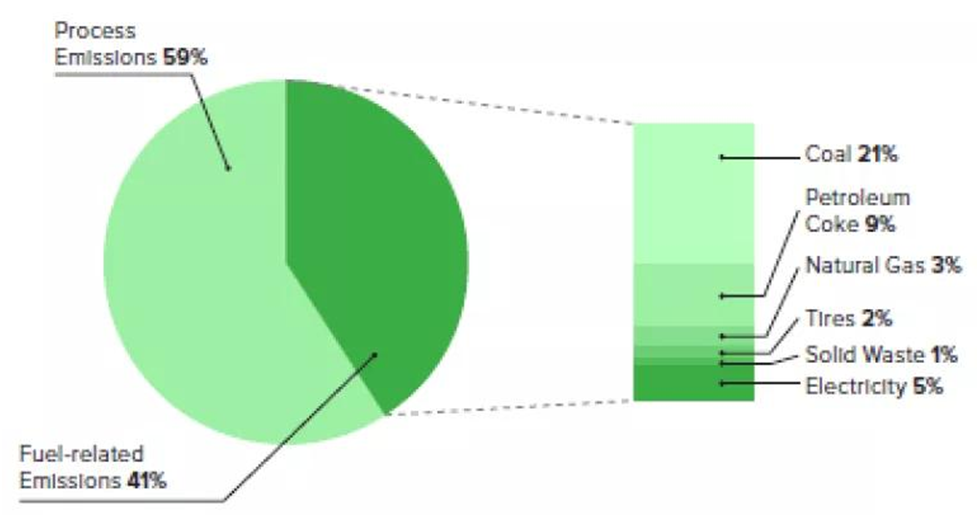
The roasting (calcination) process liberates CO2 from limestone to give quicklime: a key resource in making cement clinkers. The process is energy intensive and temperatures can be as high as 1450 °C.
Solid waste management and the cement industry
Another major area where the cement industry contributes negatively to environmental sustainability is in the release of large amounts of solid waste into the environment. This is inevitable considering the astronomical volumes of solid dealt with in the manufacturing process.
The solid wastes released in the cement industry includes rock spoil, fly ash, kiln dusts and other solid particulates. Such suspended particles in air have adverse health effects. It has been shown to have a correlation with illnesses such as pneumonia, asthma, chronic bronchitis/emphysema, and lung cancer.
Moreover, the activities linked to harvesting of raw materials for cement manufacturing, damages the green landscape which is the habitat of flora and fauna exposing to the risk of ecological imbalance.
How the Impact of Cement Manufacturing on Environment can be Minimised?
Techniques such as carbon capture and storage (CCS), material substitution, alternative fuels and energy efficient technologies have been proposed as means of mitigating the negative environmental impact of cement production.
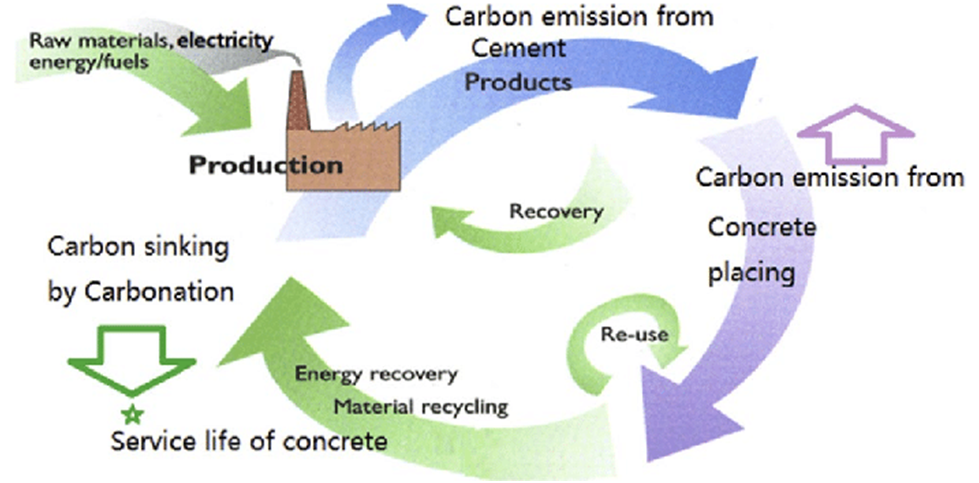
Cutting the clinker
Clinker is the primary component in cement and is extremely carbon-intensive, making up 90% of overall emissions from cement.
Replacing clinker with supplementary cementitious materials (SCMs) that are less carbon intensive directly tackles process-related emissions, but no existing commercialized solutions exist that can completely replace clinker at scale.
However, there are a number of proven ways to significantly reduce the amount of clinker needed to make cement and concrete, and one of the most promising solutions is called LC3 – Limestone Calcined Clay Cement – which can reduce CO2 emissions by around 40% compared with conventional cement.
LC3 addresses both sources of carbon emissions from making clinker. First by replacing half of the clinker with calcined clay and ground limestone, neither of which releases carbon when heated the way limestone does. Second, the clay is heated to a much lower temperature, which reduces the amount of fuel required and means electricity can be used instead of fossil fuels.
Replacing limestone
The heating of limestone to produce clinker accounts for 50% of emissions in cement production.
So alternative chemistries and processes that replace limestone from the clinker-production process provide a significant way to cut emissions. For example, making cement from carbon-free calcium silicate rocks – which can be found in abundance at the surface of every continent in the world – instead of limestone.
Fuel switching and electrification
Fuel switching and electrification are critical to lowering energy-related emissions.
Partially heating up the kiln used to make clinker with a decarbonized electricity source and replacing fossil fuels with low-carbon fuel alternatives for the remaining part can help phase out coal. Another approach to achieve the very high temperatures required is concentrated solar.
Capturing carbon
Point-source carbon capture, where CO2 from large sources such as power plants and industrial facilities is trapped and stored to prevent it from being released into the atmosphere, is a key method for cutting emissions in the cement and concrete industry.
Projections by the Global Cement and Concrete Association show that carbon capture, utilization, and storage (CCUS) could reduce carbon emissions by 36%, making it the largest lever to reduce the cement industry’s emissions.
Must read: Carbon capture and storage
Net-zero cement production
At COP28 in Dubai (in year 2023), countries agreed to launch the Cement and Concrete Breakthrough initiative, which strives to make near-zero-emission cement production established and growing in every region of the world by 2030.
For this goal to become a reality, the widespread adoption of innovative cement and concrete production processes such as the four listed above will be essential.
Put simply, cleaning up the cement industry is critical to achieving our climate and health goals. But unlike the internal combustion engine, cement has no readily available replacement that can scale quickly enough to meet the imperatives of the climate emergency.
Therefore, while reducing and substituting Portland cement using existing and emerging alternatives can and must be a priority, our dependence on the material will not only continue but likely grow in the coming decades—the timeframe most critical to climate action—as urbanization and infrastructure renewal ramp up. This makes it essential that we support innovation that ensures cement makers adapt to a clean future.
PRACTICE QUESTIONS
QUES . Consider the following statements: UPSC PRELIMS 2025
Statement I: Studies indicate that carbon dioxide emissions from cement industry account for more than 5% of global carbon emissions.
Statement II: Silica-bearing clay is mixed with limestone while manufacturing cement.
Statement III: Limestone is converted into lime during clinker production for cement manufacturing.
Which one of the following is correct in respect of the above statements?
(a) Both Statement II and Statement III are correct and both of them explain Statement I
(b) Both Statement II and Statement III are correct but only one of them explains Statement I
(c) Only one of the Statements II and III is correct and that explains Statement I
(d) Neither Statement II nor Statement III is correct
Answer – (a)